Oh Kanata!
July 19, 2021
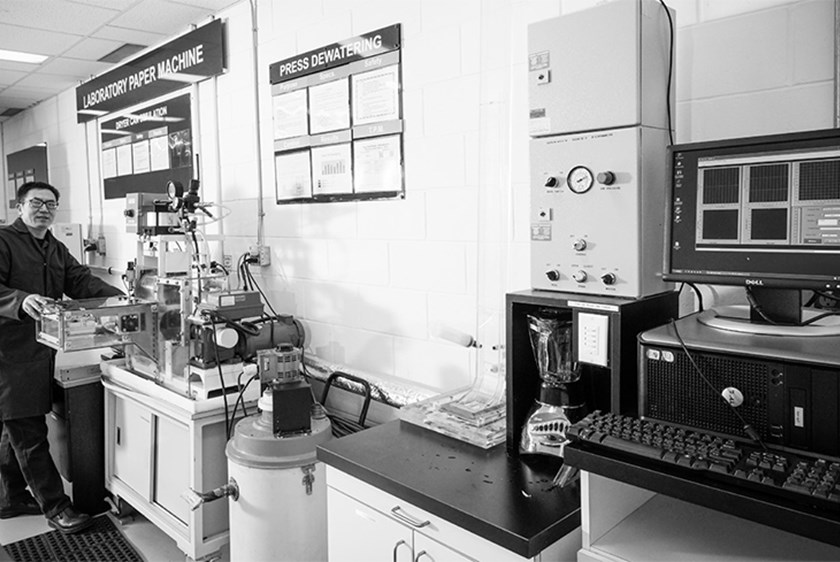
The Advanced Product Development facility in Kanata, Ontario (Canada), is a think tank of sorts: an exciting, experimental environment that centers around technical support for AstenJohnson products and the development of new solutions.
Allan Manninen is Business Leader for Advanced Products and manages a diverse group of professionals from various backgrounds and cultures. These differences are a huge asset, Manninen maintains, as they bring to light many ways of solving a problem. “We all share the goal of making a papermaker’s job easier and better,” he explains. “That’s our common focus and why we work so well together.”
Stage-Gate and a “sixth sense”
At any given time, there are perhaps a dozen key development projects underway in Kanata. By using a lean version of the Stage-Gate development process — a disciplined way of moving a project from idea to launch — the risks are reduced. And this is where the practical experience that the Kanata team has gained by testing existing products is so crucial. As Manninen explains, “In the lab, you can make a ‘perfect’ fabric and a ‘perfect’ seam due to the small sizes you are working with. In a manufacturing plant, and on the paper machine itself, things can be different. Having that sixth sense about when we can move out of the lab and into the field is what sets our team apart.”
A peek under the tent
While much of the work at Kanata APD is proprietary, there are things the team is excited to talk about.
One is the Lab-scale Paper Machine, including a gravity sheet former, two-roll press, and dryer simulator. “Using this machine,” Manninen says, “we can make a paper sheet and evaluate the drainage of the forming fabric, dewatering of the press felt, and drying rate of dryer fabric all in one flow.”
Another is PresSym™, a press nip simulation program used to visualize and understand the effects of press dewatering. “Pressing can be quite complex,” explains Dr. John Xu, APD Specialist. “We combined the underlying theory and various mathematical models into a single, comprehensive model, which we call PresSym.” AstenJohnson associates use PresSym to model a specific customer machine, inputting different values for speeds, nip pressures, basis weights, etc. to accurately predict what the outcome will be on the machine.
Still another development is the Seam Quality Index (SQI) tool, a combination of a high-tech scanning system and proprietary computer code to validate seam quality on press felts. “With SQI, we analyze seam pressures and have developed an index to classify seams,” says Dr. Jenny Zhou, APD Specialist. “We have now built up a sizable database of knowledge about seam marking.” The SQI tool is utilized by press fabric designers to evaluate different seaming approaches and technologies to eliminate any marking of the sheet for various applications as much as possible.
In a similar vein, Kanata APD developed a proprietary Print Quality Index (PQI) that has proven to be a reliable indicator of the printability of a sheet. “By analyzing variations in sheet density over a relatively small area (micro-density uniformity), we have created a useful tool for forming fabric designers to use in paper grades and applications where print quality is critical,” says Derek Chaplin, APD Specialist.