Removing Contaminants and Cutting Costs : Smart Surface Keeps Fabrics Clean
October 24, 2018
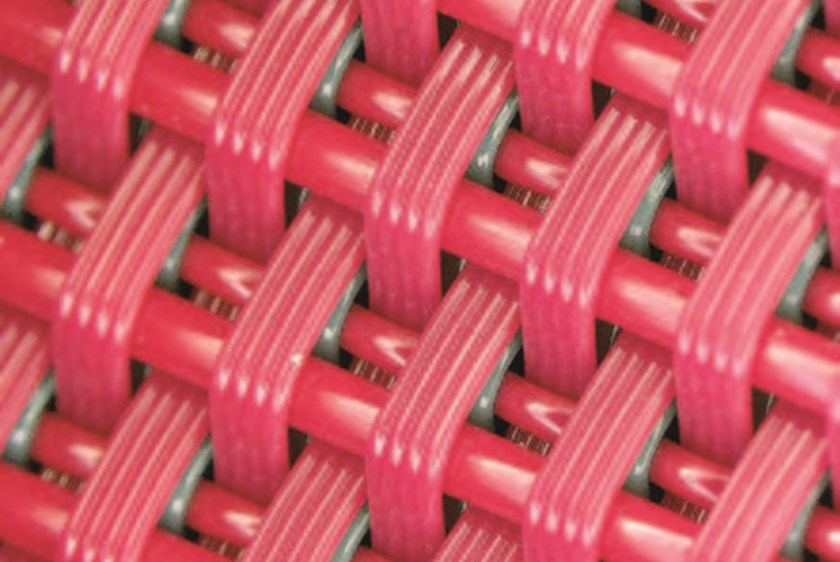
Keeping a dryer fabric clean has always been a concern for papermakers. With the widespread use of recycled fibers, the concern has grown. When contaminants become lodged in the fabric’s pores, they reduce the drying capacity of the fabric. However, frequent cleanings also come at considerable cost and energy.
Hills and valleys
AstenJohnson introduced its first innovation to improve the cleanability of dryer fabrics in 2006 with Smart Surface Technology™ (SST). The solution was radical at the time: do away with large, flat surfaces on the fabric yarns and instead create more smaller contact areas. This was achieved by creating tiny grooves the length of the flat ribbon yarns. Small contaminants land on top of the grooves (the “hills”) but detach easily. The grooves’ “valleys” form perfect channels for shower water to wash contaminants away.
Multiple Options, Multiple Ways to Save
Recent breakthroughs expand on the SST line by altering the fabric surface, moving the “neutral line” within the fabric to minimize stretch and draw, and creating a thin, single-layer design to provide unmatched stability and life. These advancements save money in multiple ways. First, by preserving the air permeability of the fabric throughout its life, a papermaker can tally significant energy savings. Next, by requiring less frequent cleanings. And finally, mills can keep the fabric on the machine longer and reduce operating costs.
The MicroTec™ fabric is symmetrical in that the paper side and machine side are equal when viewing a cross-section of the weave. This begged a question among AJ engineers: can the performance be fine-tuned for different grades and different machines as the neutral line shifts up or down?
In short, absolutely. SpeedTec™ was born when the neutral line was shifted closer to the sheet side in order to minimize stretch and draw forces on the sheet as it passes around the top and bottom dryer cans. This is especially important on high-speed machines. Shifting the neutral line in the other direction, and creating a “knuckled” surface on the yarns in addition to the SST grooves, resulted in the creation of CleanTec.™
In its first field trial, CleanTec was installed on a high-speed packaging machine in the sixth dryer position. The dirt accumulation was dramatically reduced compared to previous fabrics, and the lifetime on the machine was doubled. The latest innovation is MagnaTec,™ which uses new weaves and materials to produce a single-layer dryer fabric that is robust enough for early dryer positions. MagnaTec has the best wear volume of any dryer fabric in the industry. And the single-layer structure has less void, maintaining the SST reputation for easier cleaning.
*Featured Image: CleanTec™ "knuckled" grooves reduce the accumulation of contaminants.